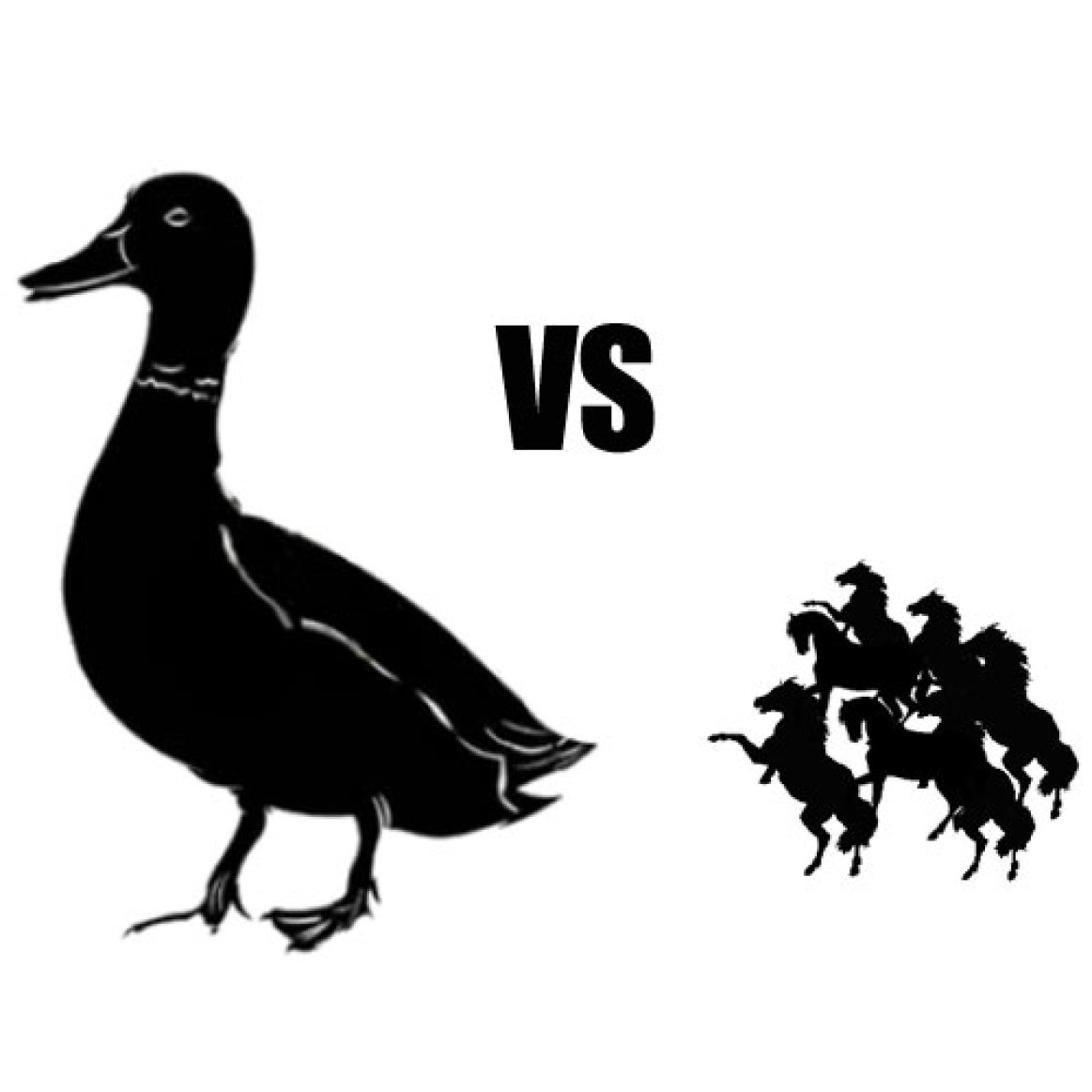
In December last year, Greentech Renewables published an article on the emergence of tier 1 UL listed AC modules and their applicability for projects when compared to String Inverters, DC Optimizers and Microinverters. The article focused on projects ranging from small residential in size, up to large commercial.
The latest trend in commercial, large commercial and small utility scale projects in the US takes the next step with string inverters vs. central inverters. When is it best to distribute power conversion over a site instead of focusing it at one point?
In a perfect world (for PV) there would be a wide open field with a gentle wind to maintain an even 75 degree F. temperature across the entire array, no shading and no need for disconnecting, smart, arc fault detecting (AFDI) or other combiner box embellishments. The central inverter would be cheap and reliable and perfectly match the required size of the Power Purchase Agreement.
If the above scenario doesn’t apply to a project, then here are some simple guidelines for a few of the conditions that might warrant a Distributed Generation (DG) approach:
- Obstructions or geographical factors that might cause uneven temperatures in the array – DG breaks the array up into ‘microclimates’ and allows MPPT to occur on a more granular scale.
- Intermittent shading from trees, poles or other obstructions – again, DG lessens the overall effect on output, just like microinverters or DC optimizers.
- No obvious place for a concrete inverter pad or security reasons for keeping equipment on the roof – DG allows all equipment handling to be done with the same equipment that is used for placing modules. Most DG inverters can be handled by two people and can also be mounted on the actual PV racking.
- A requirement for combiner or “zone” level intelligence or safety infrastructure – DG can provide disconnecting, monitoring and AFDI, usually as a drop in replacement for the central inverter combiner boxes.
- Performance guarantee or downtime penalties for an inverter failure – DG completely avoids the risk of site shutdown in the event of an inverter failure and greatly lessens the repair time for inverter repair / replacement.
Like the enigmatic Duck-sized horse question, there are obviously counter arguments to the above points – but DG is another useful architecture that can answer many of concerns that could stand in the way of a problematic PV project. The DG architecture has proven so effective that many hundreds of megawatts have been built in Europe over the past few years and we are likely to see its proliferation in the US as well.