
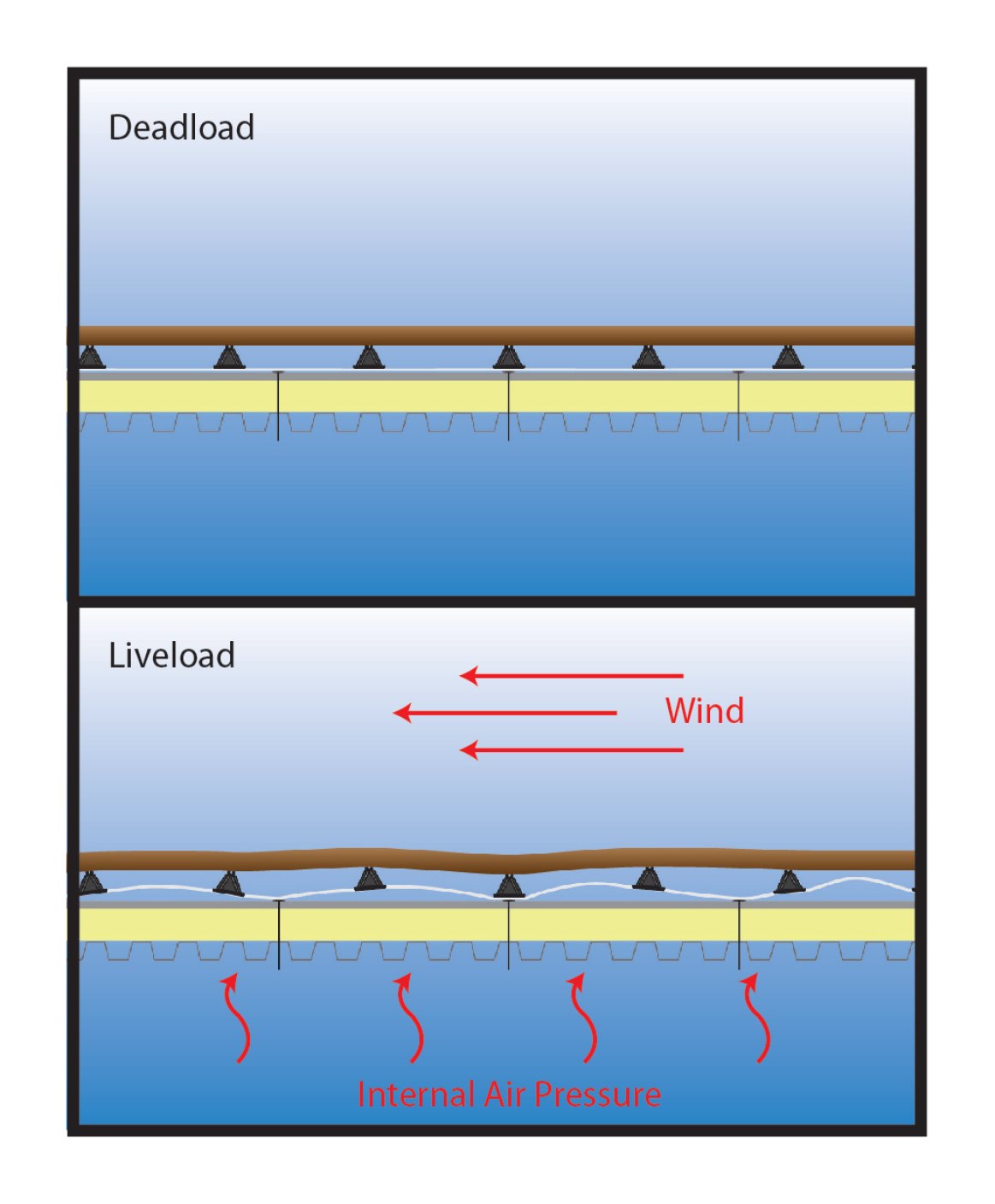
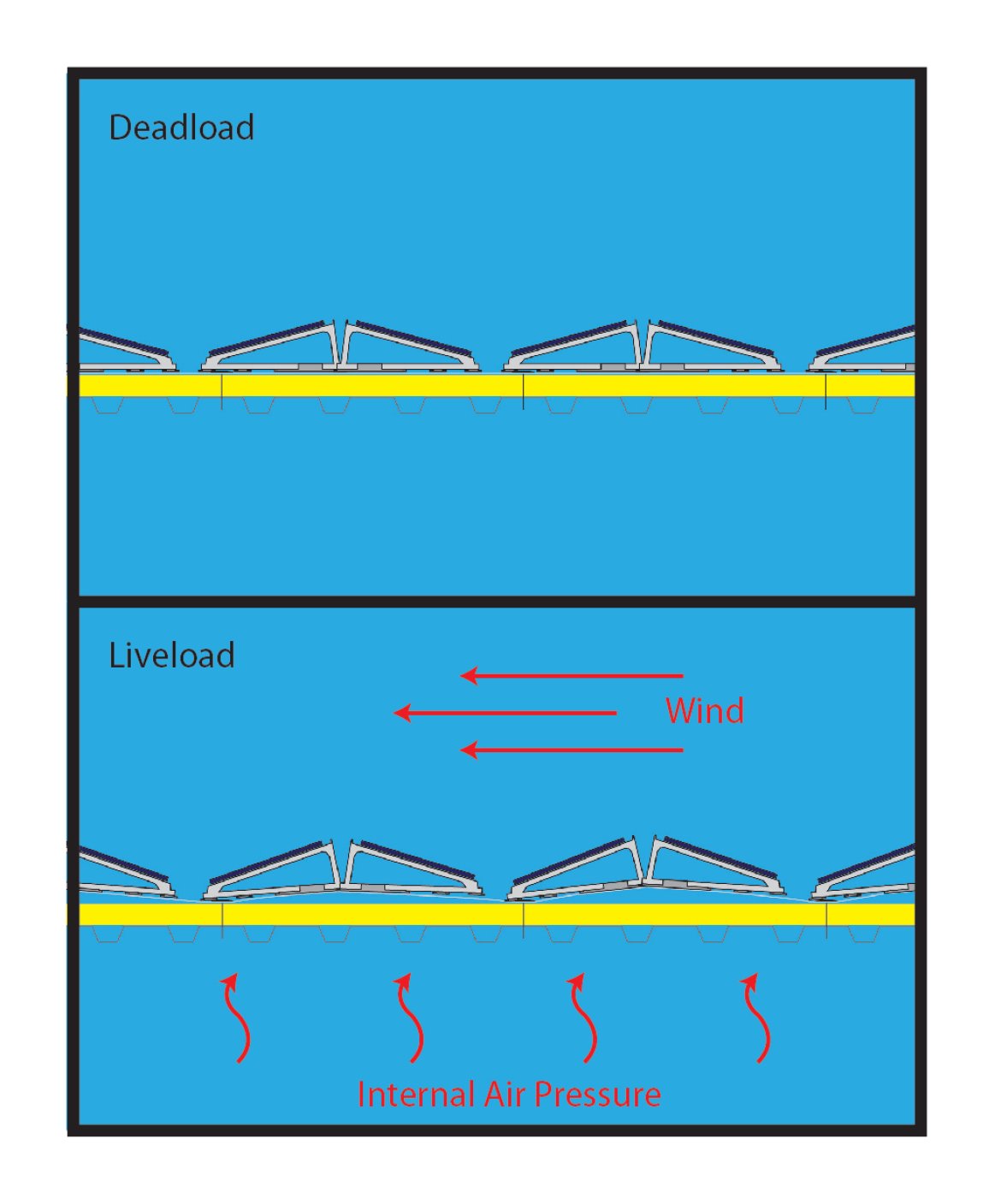
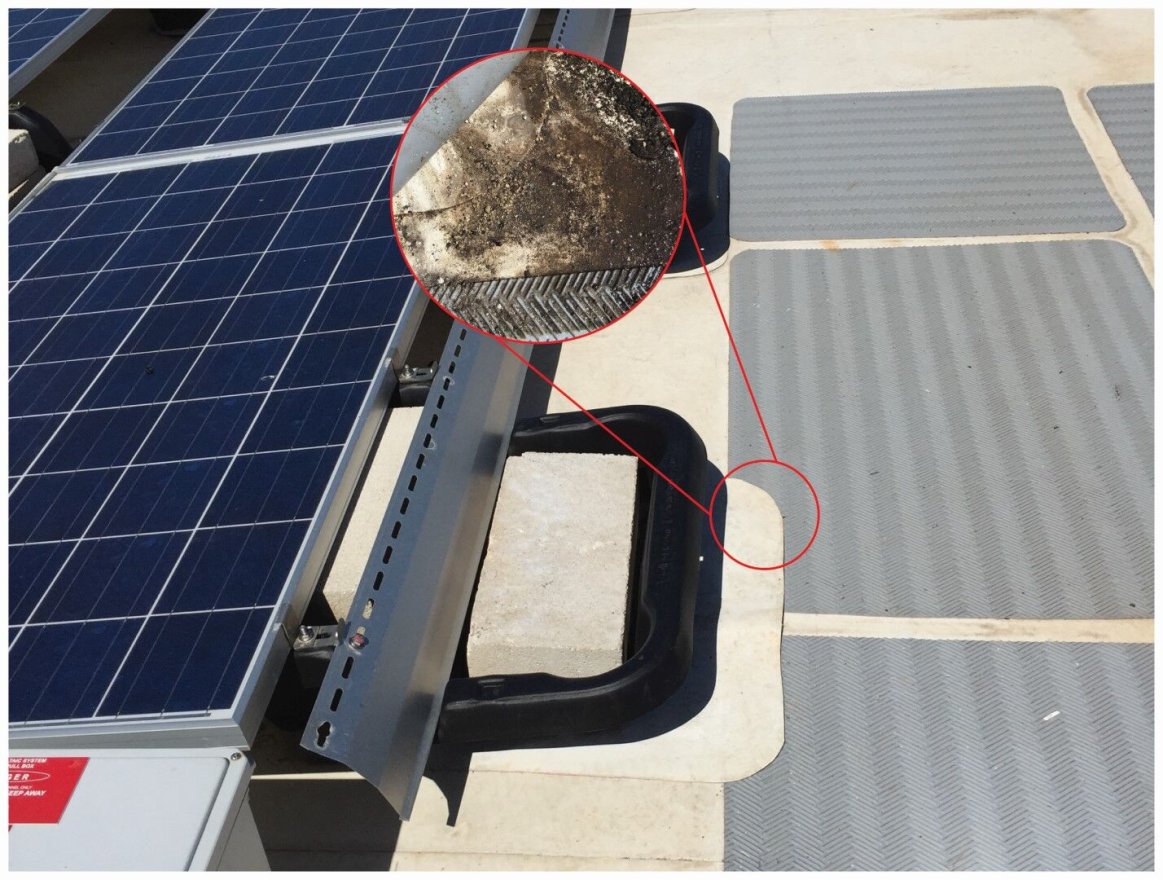
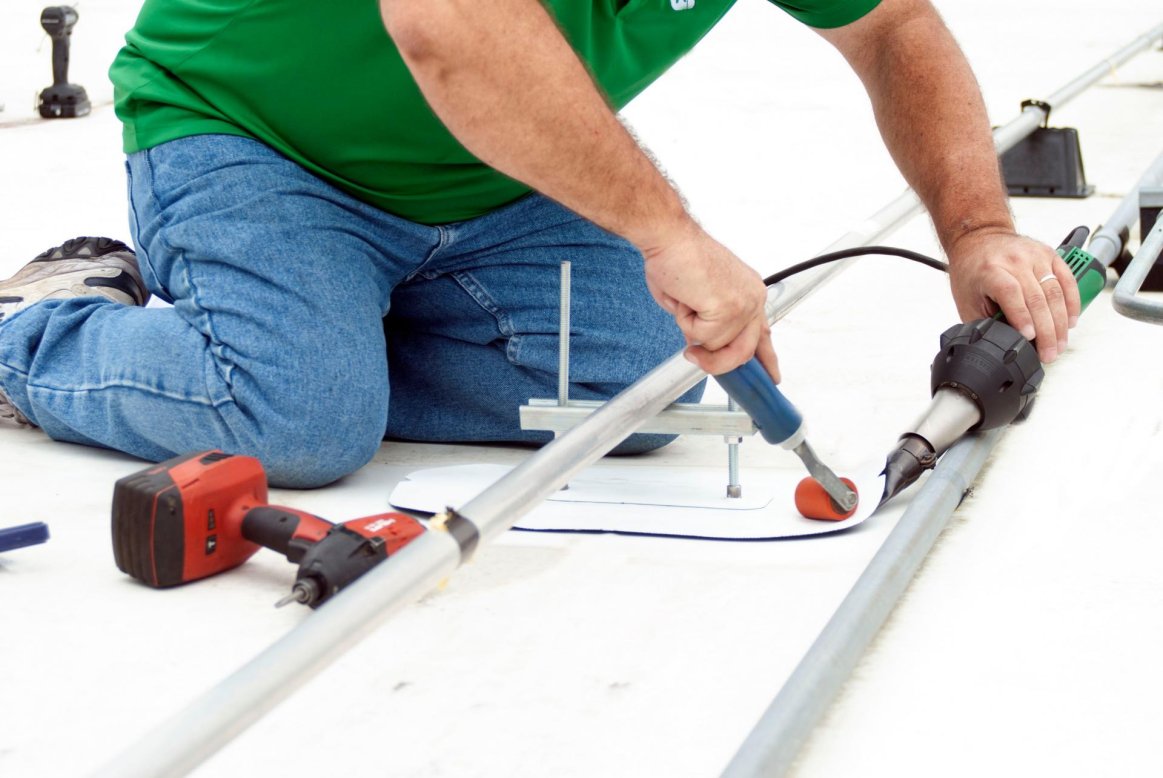
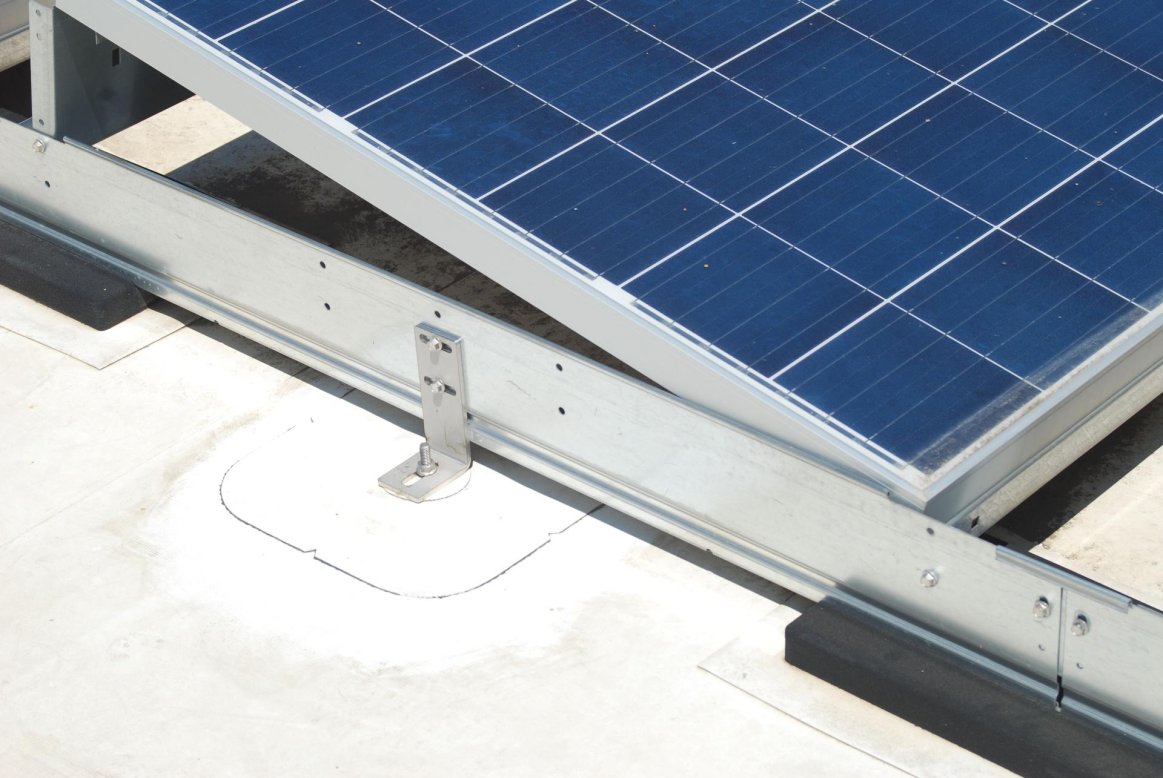
The roof of any structure is a delicate thing. Add in the many system and equipment components that sit atop roofs such as solar panels, antennas, satellite dishes, and HVAC systems, and it really becomes complicated. But unless the dynamics of a roof and proper roof practices are understood, the integrity of the roof can easily be compromised in many ways.
Like any equipment placed on the roof, they are exposed to elements such as rain, snow, intense UV exposure, extreme cold, and (one of the most damaging) wind. Wind has a tremendous impact on rooftop equipment. These pieces of equipment need to be secured to the roof properly to prevent them from blowing off – and a ballast block has been a common way to do this.
Historically, ballast blocks have been the go-to for non-roofing trades when installing equipment, as it is assumed that as long as they don’t make any holes in the roof, all is good. And while it’s easy and convenient to place a concrete block into a ballast tray, it can cause severe damage to a roof and structure. Additionally, there is no direct attachment to the roof and therefore movement will occur.
Dead Loads Turning Into Live Loads
The composition of a ballast is very simple and straightforward – it is made of concrete (which is heavy), it is compact (and heavy), and tends to stay put (because its heavy). So of course, it would seem like an ideal solution for weighing something down and not letting it budge an inch.
When a ballast block is placed on a roof to “secure” the equipment down, it is typically calculated as a dead load. This means that the engineer running the load calculations for the system being installed is seeing the block as an object that will not move. Unfortunately, the overwhelming majority of roofs installed today are mechanically attached. And the overwhelming majority of those roofs are single-ply membranes. Mechanically attached single-ply roofs utilize a fastener and plate combination down the seams of the roofing membrane. Therefore, the center of the sheet is simply laying out and not attached. During a wind event, there is an effect referred to as billowing. This occurs in two ways: 1) when air travels across the surface of the roof, it creates lift (much like an airplane wing) and lifts the unattached membrane off the roof, 2) air inside the building is pushed up through the gaps and holes of the roof deck and essentially inflates the membrane. Often, these two ways occur simultaneously. See a billowing roof in action.
Now why is this important? An average 60mph sustained wind is not uncommon, yet it is easily powerful enough to lift a 200lbs person standing on the roof. The person was considered a dead load (much like the ballast block) until the wind and membrane lifted them off turning them into a live load. The continuous lifting and falling of a ballast block will damage the roof over time and the wind load calculations for the equipment are not correct anymore. For example, the 5-degree tilt on the solar panel was 5 degrees until the storm that rolled through caused the membrane to lift it several inches off the roof. This type of change risks having the equipment damaged, come loose, or fall off the roof.
Structural Limitations And Impacts
There is a fundamental flaw that few realize. Roofs were made to keep water out and not necessarily to support massive amounts of weight. And when weight is added to a roof, it needs to be distributed evenly across the roof to ensure that it does not break through and fall. Engineering, of course, accounts for the limitations of the structure when planning a project, but they are limited when only utilizing a block to hold their equipment. More and more, hybrid applications that use both ballast and attachments are being utilized to address the structural requirements, but that addresses part of the problem.
When it comes to the installation of ballast on a roof, the cost of that heavy little block starts to rise dramatically. When ballast blocks are delivered to a job site, its palletized. To get it from the truck that delivered it to the roof, you either need a crane or some other equipment to lift it up to the roof. Depending on the size of the project, that equipment can be there all day or even all week as you simply cannot put a full pallet of blocks in one spot of the roof. That would point load the roof beyond its limits and eventually fall through.
Installers then have to relocate the ballast to its specified location. One method requires a cart. While the cart is potentially faster and easier, it can easily destroy the materials underneath the membrane (coverboard, insulation, etc.) as it wheels across it. Another primary method is to carry each block by hand. This definitely reduces the strain on the roofing system, but it opens up the opportunity for dropping the block – which is not a cheap repair.
Once the blocks are in place and you’ve managed to avoid damaging the roof in the process, there’s still another long-term issue that occurs – sagging. Over time, subtle and natural movements of the building from expansion and contraction causes sagging in areas where the majority of weight is which greatly impacts the roof’s ability to shed water. Sagging leads to ponding water areas. Ponding water rapidly degrades the roofing systems because it’s not just water that is pooling. Rather, it’s the product of its environment. The acidity of the rain itself, the chemicals that may already be up there, and even the chemicals from cleaners that are used to keep solar panels at their optimum production level. Overtime as the water evaporates and then re-pools, the chemical concentration becomes more toxic to the roof system. This doesn’t happen overnight, but it can decrease the lifetime of a roof dramatically, which is typically 20 to 30 years.
Ballast Block Lifecycle
As durable as a solid block of concrete may seem today, exposing it to the elements repeatedly and for extended periods of time takes a major toll. Ballast blocks break down during their life and become significantly smaller particles. Roofing manufacturers refer to this process as “sluffing” and the debris that results from sluffing is called “aggregate”. This aggregate tends to be jagged little pieces that dig into the roof when a maintenance guy walks across it. The aggregate may also be trapped underneath equipment, such as an HVAC unit, which creates a vibration when it turns on that creates holes. Yes, the vibrations may seem minimal and there’s not much movement. But keep in mind a vibrating sander does not move much either, yet it rips off the top layer of wood in an instant. Imagine that happening day after day on a roof.
These will eventually cause leaks, which are almost impossible to trace. To service the roof, the ballast and equipment would have to be removed. Furthermore, it will certainly void any roof warranty as the foreign material (the ballast block aggregate) was not originally on the roof or covered under the warranty. It’s a very time intensive process and can be extremely costly to building owners.
U-Anchors Deliver Superior Performance
The better alternative to ballast blocks is a U-Anchor. U-Anchors integrate flawlessly into the roofing system as they are installed exactly like the rest of the roof. U-Anchors are minimally invasive, install rapidly, do not void the warranty, last longer, and tend to cost less overall than using ballast.
U-Anchors use the specific type of roofing material needed, from the specific manufacturer needed, and are available in the color needed on each project. U-Anchors provide a direct path of attachment from the equipment, to the U-Anchor, and down to the deck of the roof, providing consistent performance that stands up to wind and seismic conditions. With the U-Anchor, you have a lighter, smarter, and more efficient alternative. U-Anchors protect roofs and your investment. Learn more about U-Anchors to design your next project with the best attachment solution on the market.