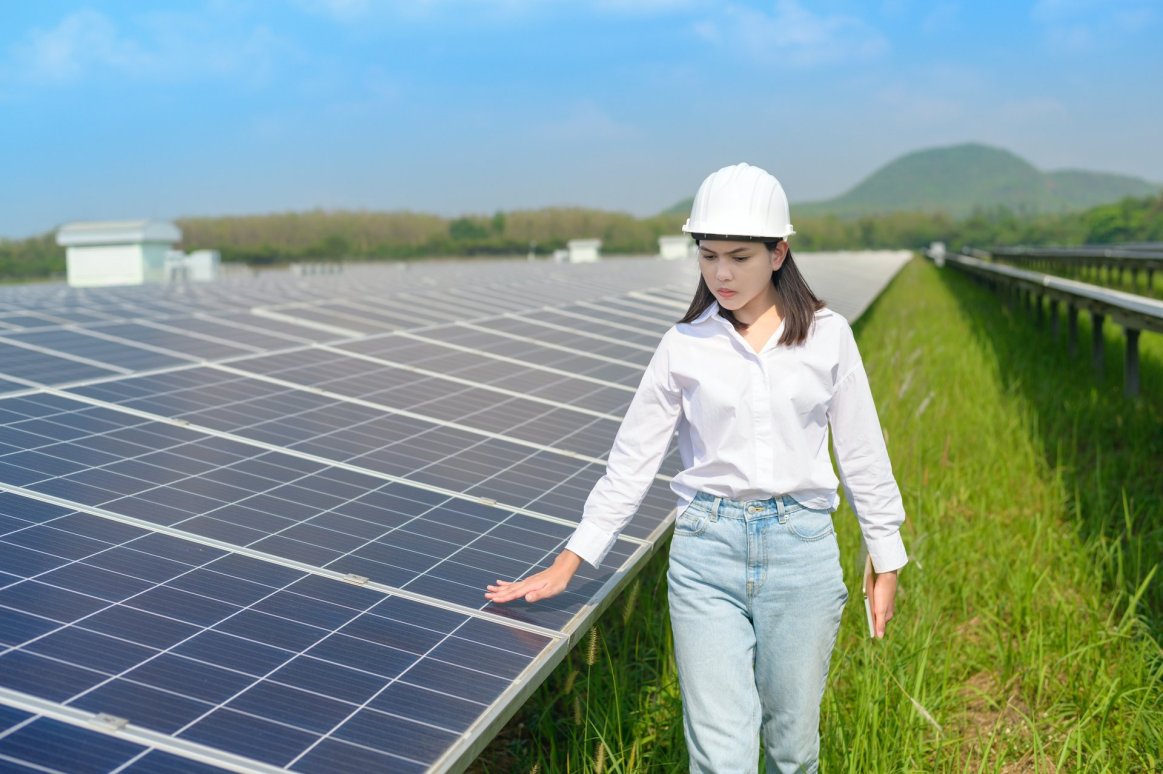
Frame
The frame gives the solar panel shape and stability and protects the glass top layer from damage by flexion. Anodized aluminum is the best frame material to achieve shape and stability. JinkoSolar extrudes its own frames using aircraft grade aluminum to ensure panels are some of the most durable on the market.
Glass
Glass typically forms the top layer of the solar panel. Glass provides mechanical strength, protects the solar panel’s front surface from physical damage and allows light to reach the solar cells. Tempered, low-iron glass, which is the type JinkoSolar uses, is a preferred type of glass. Tempered glass is manufactured using a heat-treatment process that results in a glass that is on average four times more resistant to breakage than untreated glass. Low-iron glass has a minimal tint and high clarity. It allows greater light transmittance than conventional glass (approximately 91% vs. 83% for conventional glass).
Encapsulant
The encapsulant is a polymer envelope that surrounds the solar cells, protecting them from UV damage and weathering while permitting broad-band light transmission. The encapsulant cushions and protects the fragile cells and the delicate circuitry within. In its 72-cell modules, JinkoSolar has developed an encapsulant called white EVA, which goes on the backside of the solar cells. In traditional encapsulant, the film is clear, thus allowing light to pass through. In JinkoSolar’s white EVA, light is reflected back into the cell, thus helping it generate more power.
Ionomer film is the preferred encapsulant material. It is easy to laminate and has a low shrinkage rate. It also has the strong adhesion and elasticity properties required for solar cell encapsulation. Encapsulant materials should be UV-stable; prolonged UV exposure can cause browning of non-UV stable encapsulants, reducing light transmittance over time.
Solar Cells
The solar cell is the beating heart of the solar panel and the basic unit of energy production. A cell consists of one or two layers of silicon-based semiconductor material. Electricity is produced when energy particles from the sun, called photons, strike the silicon, knocking electrons free and causing them to flow from one side of the cell to the other. This movement of electrons creates an electrical current, which is then carried outside of the cell by metallization pastes. Usually made with silver, metallization pastes are screen printed onto the surface of solar cells. Metallization pastes collect the electricity produced by the cells and transport it out. DuPont produces a silver paste called Solamet®, which JinkoSolar uses in 100% of its modules in order to boost power output. Each gain in efficiency reduces balance of system costs because less area is needed to generate the same power, installation and structural costs are lower, and operation and maintenance costs are reduced. DuPont and JinkoSolar are working closely together to optimize cell performance using the Solamet® silver pastes.
Solar cells are created from ingots and wafers. JinkoSolar produces the largest capacity of ingot and wafer manufacturing among vertically integrated suppliers. JinkoSolar’s cells are also the world’s first to be certified to be free of potential induced degradation (PID). PID occurs when the module’s voltage potential and leakage current drive ion mobility within the module between the semiconductor material and other elements of the module, such as the frame, thus causing the module’s power capacity to degrade. Humidity, temperature, and voltage potential all increase those risks. By bolstering its cells, JinkoSolar’s advanced R&D division found a cost-effective way to prevent these stray currents from occurring, thus guaranteeing the power promised on the nameplate.
JinkoSolar currently produces both polycrystalline and monocrystalline cells, with the ability to add passivated emitter rear contact (PERC) technology to its monocrystalline cells. This extra reflective layer on the backside of the cell allows more light to be absorbed into the solar cell, thus generating even higher output. As one of the most sophisticated manufacturers in the world, JinkoSolar is constantly looking for new ways to increase power, while remaining cost-competitive.
Backsheet
The backsheet forms the back, or outermost layer, of the solar panel. Some early solar panels were made with glass backings, but polymer laminate materials have proven more design-friendly, dependable, and cost effective. The backsheet plays a vital role in protecting the photovoltaic cells from external stresses, including UV radiation, temperature fluctuations and moisture ingress. The backsheet also serves as electrical insulation, an important safety role, and therefore must have high dielectric properties. Durable polyvinyl fluoride (PVF) films, such as DuPont Tedlar®, are used in 100% of JinkoSolar’s modules, are a preferred backsheet material. They are proven to protect solar panels for more than 30 years, even in extreme outdoor conditions.
Junction Box
The solar panel’s individual strings come together at the junction box. The junction box protects these wires, which then carry the current produced by the solar panel to an inverter, where direct current (DC) is converted to the alternating current (AC) used by most household appliances. Most junction boxes are assembled with diodes, which keep the electric current flowing in one direction (out), and prevent power from feeding back into the panels. A quality junction box must be watertight and thus able to keep corrosion at the terminals to a minimum. Waterproofness is represented by an IP (Ingress Protection) rating. A completely water tight junction box carries an IP rating of 67. Junction boxes should be made with UV-resistant polymer resins and be capable of meeting all known thermal requirements.
JinkoSolar is one of the only panel manufacturers that manufactures its own junction boxes. Most junction boxes are outsourced to third parties. With this ability, JinkoSolar not only reduces the cost of the junction box, but also maintains strict control over a component of the panel that is often overlooked and less scrutinized.
Greentech Renewables prides itself in delivering the most reliable modules on the market, and together with JinkoSolar and DuPont Photovoltaic Solutions believe that Materials MatterTM. Both JinkoSolar and DuPont’s materials have been repeatedly verified by third party testing and field testing to perform over time, which means reliable investment returns for you. Whatever your needs, JinkoSolar and DuPont deliver the performance, efficiency, and value Greentech Renewables contractors require day after day.
To learn more about what makes a durable solar panel and why we choose the manufacturing partners we do, talk to your Account Manager today.