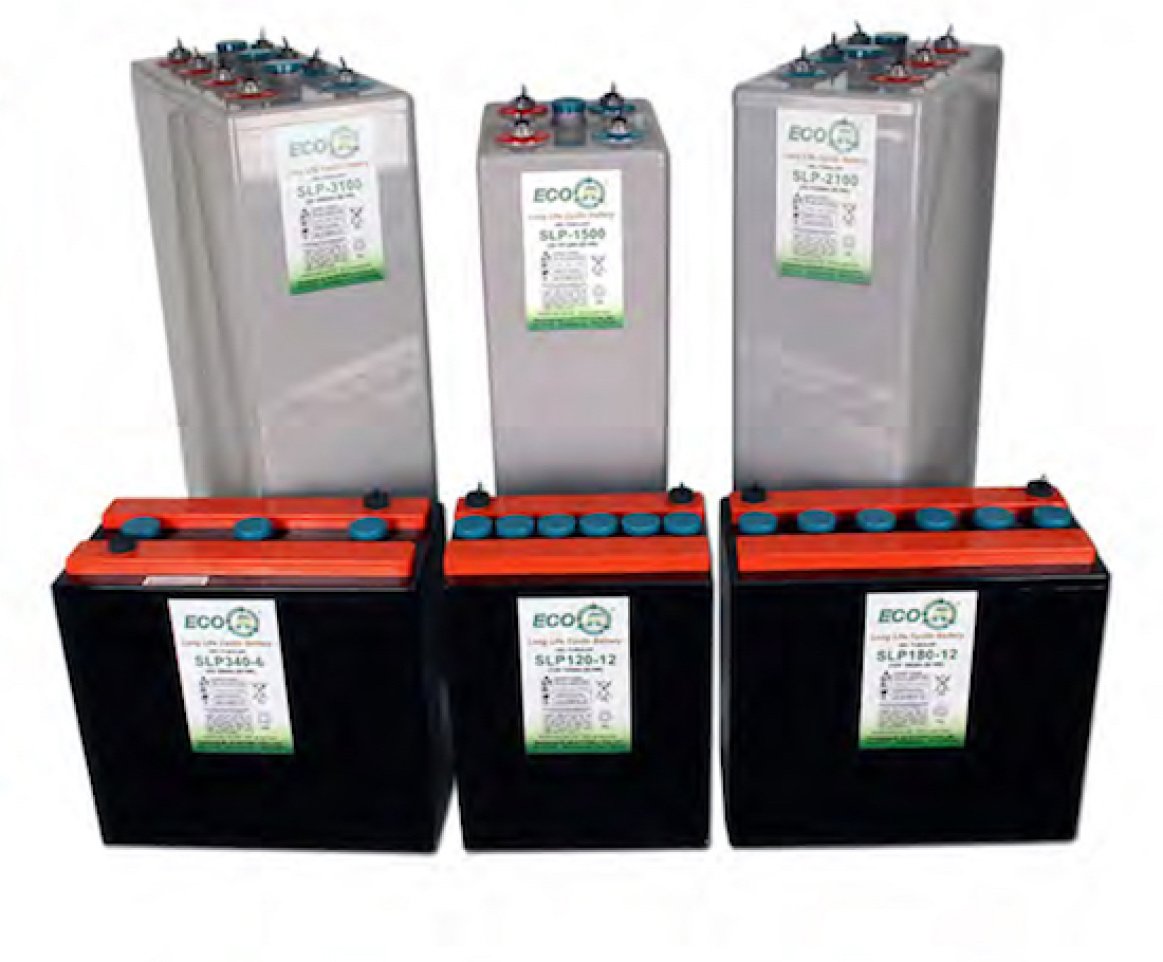
Lead-Acid batteries are still the most common form of energy storage for photovoltaic systems. A lead-acid battery charges, stores, and discharges energy based on a chemical reaction of the metal that makes up the plates. The plates are in an acid that serves as the electrolyte to provide electrons that participate in the reactions. Lead-acid batteries can be easily recycled (99% of lead from used batteries is reclaimed) The reactions are as follows:
O2 + 2Pb → 2PbO
Pb + H2SO4- → PbSO4 + H+ + 2e-
PbO2 + HSO4- + 3H+ +e- → PbSO4 + 2H2O
These are reversible reactions that proceed in one direction when the battery is charging and in the other when it is discharging. The battery cycles by proceeding back and forth through these reactions repeatedly. The more times that the battery goes through these cycles, the more the state of health of the battery gradually deteriorates. Most batteries are considered to be at their end of life when they reach 80% of their initial, fully charged amp hour (Ah) capacity.
To incorporate larger quantities of intermittent renewable energy resources, tomorrow’s electric grid will require far more energy storage capacity. Traditionally, lead-acid batteries have been reserved for backup power and off-grid applications. This is in part due to the cycling limitations of the lead-acid chemistry. As a battery cycles from a charged to discharged state, and then back to fully charged state, lead and lead dioxide react with sulfuric acid within the battery, producing lead sulfate. This process is known as sulfation. Over time these crystalline sulfate deposits accumulate on the negative electrodes in the battery, thereby preventing the battery from returning to a full state of charge. Sulfation is exacerbated by high current discharge from a partial state of charge, a common ask of grid-scale energy storage.
Carbon Lead-Acid: A Battery To Meet Demand
Are lead-acid batteries forever relegated to small off-grid and residential applications? Not anymore. In 1997, research uncovered that by adding carbon to the negative electrodes of a battery dramatically decreases the degree of sulfation. Improvements to battery performance under high-rate partial-state-of-charge operation is also another benefit of carbon integration. Altogether, this means more cycles and a longer service life.
One manufacturer to embrace this technology is GS Battery. At 70% depth of discharge, the GS SLR-1000 achieves 5000 cycles. These qualities make the GS battery a good choice for both battery backup and off-grid solar applications. Carbon can be incorporated into the lead-acid design in a couple different configurations. One technique involves blending carbon additives into the lead sulfate paste that makes up the negative electrodes. Alternatively, electrodes can be partially replaced with the addition of a carbon-based electrochemical capacitor. This hybrid design greatly improves cycle life over traditional lead-acid batteries.
Comments
Jack,
Simply put, scrap lead has a spot value of about $0.15 per pound ( http://www.scrapmsc.com/our-pricing/ ). The plastic and sulphuric acid are fully recoverable and can be used in new batteries after recycling. East Penn, a very large battery manufacturer, can even trap the sulphuric acid fumes and convert them to a usable ferilizer product with their advanced recovery process.
While chemistries like Lithium Iron Phosphate and others are theoretically recyclable, there is not the established scrap value chain. In fact, all other chemistries that I know of (excluding Aquion) are considered hazardous waste and have a disposal cost.
Here's a useful illustration from East Penn: http://www.dekabatteries.com/assets/base/recycling/recycling1.htmlhttp://www.dekabatteries.com/assets/base/recycling/recycling1.html