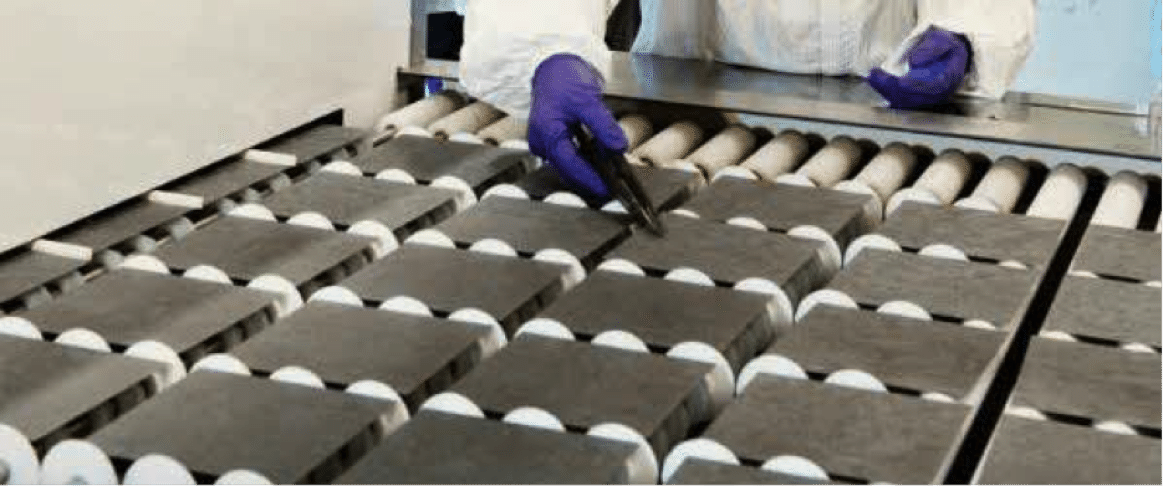
Hot on the heels of news that the industry may be in store for a wafer supply shortage Canadian Solar has announced plans for substantial near-term expansion of its silicon wafer production capacity. Solar wafers represent a vital input to producing complete solar modules. This process starts with polysilicon rock melted at nearly 2,500 degree F. Once liquefied, a small seed crystal is lowered into the rotating vat of molten rock on a cable. As the silicon solidifies on the seed crystal the cable is slowly retracted, creating a long cylindrical crystal. From here, the crystal is trimmed and cut resulting in solar wafers. At this stage the wafers are treated and circuitry is printed to prepare the wafers for assembly into modules.
Although oversupply has been the name of game in wafer and module production over the past four years, the tide is beginning to turn. As the ITC expiration inches closer, Tier-1 module manufacturers have begun to report booked capacity through the first quarter of of 2016. Nowhere will this demand be felt greater than in wafer production, as this portion of the supply chain has already been operating at 95% of capacity over the past 6 months. Despite significant investments in module manufacturing capability, far less resources have been spent on developing wafer infrastructure. Instead, some manufacturers have chosen to purchase wafers from OEM suppliers or optimizing existing production practices.
Despite this constrained outlook, Canadian Solar is set to lead the pack in 2016 by more than doubling in-house wafer production to 1 GW by the middle of next year. Additionally the company has plans to expand both cell and module manufacturing capacity by nearly 1 GW for each. By ramping up production throughout the supply chain, Canadian aims to keeps costs down and continue to meet market demand. This expansion comes not a moment too soon as both the US and China seek to add record amounts of solar this year and next.
JinkoSolar represents another vertically integrated industry leader that stands to play an increasing role in the global and domestic PV market. The firm’s newest facility recently hit peak production adding 500 MW of cell and 450 MW of module manufacturing capability. These additions come on top of the Jinko’s already impressive manufacturing potential. Jinko adds value across the supply chain with 3 GW of ingot capacity, 2.5 GW for cells and 4 GW for modules. Most recently Jink announced the addition of an integrated smart module to its lineup. By integrating maximum power point tracking (MPPT) at the cell level into an existing junction box the Smart Module maintains installation efficiency while effectively combating losses due to shading and soiling.