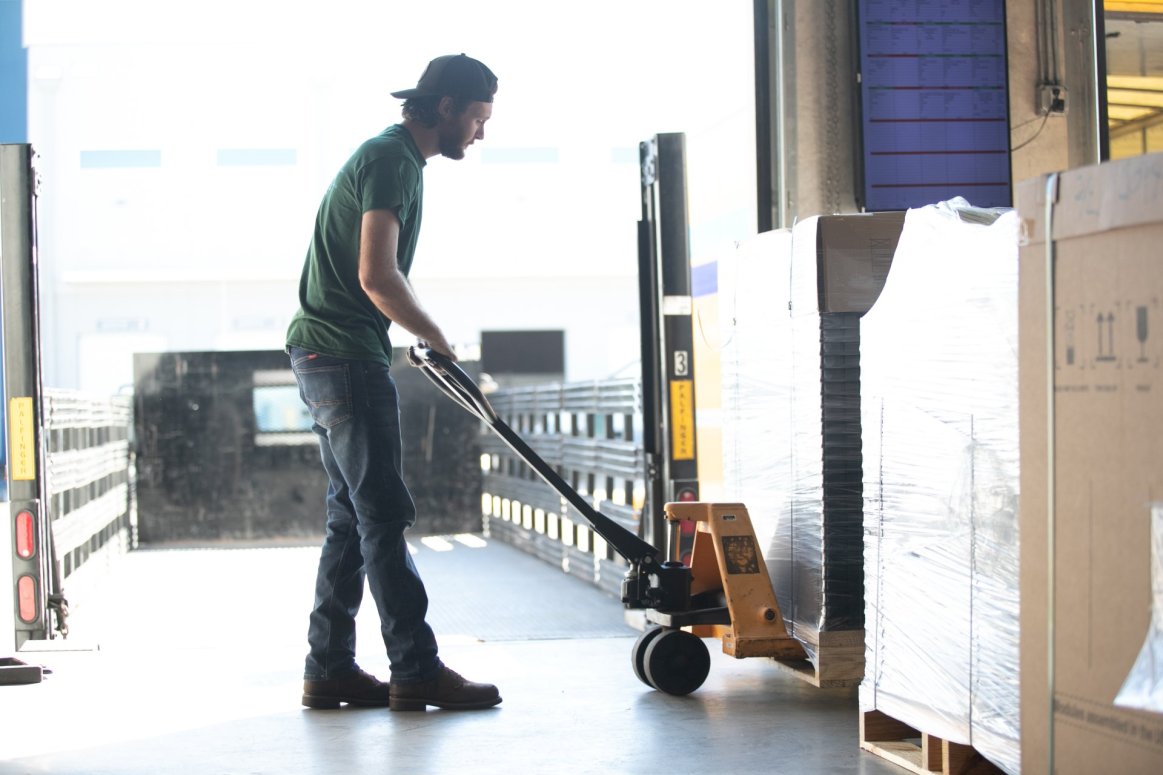
The Momentum Builds for Domestic Solar Manufacturing
The U.S. is well underway in its pursuit of onshore clean energy manufacturing. As we approach the second anniversary of the passage of the Inflation Reduction Act (IRA) of 2022, the Solar Energy Industries Association (SEIA) reports that U.S. solar and storage companies have announced more than $100 billion in private sector investment. According to SEIA, these announcements have resulted in approximately 50 new facilities or expansions. As the nation’s most trusted solar distributor, we strive to stay ahead of the curve through our innovative product solutions and services beyond supply.
Motivated to take advantage of compelling tax credits and provide offerings in the market for customers to qualify for generous domestic content tax incentive adders, several manufacturers far and wide have set clear intentions to become players in domestic production. Among them, our partner Qcells has invested $2.8 billion to establish a fully integrated solar supply chain in the U.S. from raw materials to fully assembled modules.
The Solar Module Manufacturing Process Explained
The process to create a fully finished silicon-based solar module comprises five key steps starting with the polysilicon raw material and finishing with a fully constructed module. First, ingots are extracted from raw polysilicon and are later cut into thinly sliced wafers. These wafers are then further processed to create individual solar cells, which are connected and incorporated into the final module assembly process. Finished modules are then palletized, packaged, and shipped out to customers.
Figure 1. Steps to Manufacture a Silicon-Based Solar Module
- Qcells
This complete process from ingot to finished module in the U.S. will be fully realized at Qcells’ newest manufacturing facility in Cartersville, Georgia. While Qcells began producing modules at the new Cartersville facility in April, the remainder of the supply chain manufacturing facility is projected to be completed by the end of this year. The plant will be the first vertically integrated ingot-to-module facility constructed and is intended to produce 3.3 GW of ingot, wafer, cell, and finished modules annually. This will bring Qcells’ combined capacity to 8.4 GW. According to Qcells, that’s nearly 46,000 modules produced daily, the equivalent of powering 1.3 million homes annually.
-Qcells Cartersville Supply Chain Facility Construction Progress (April 2024)
Qcells is committed to manufacturing modules sustainably through being a founding member of the Ultra Low-Carbon Solar Alliance. The polysilicon will be sourced from REC Silicon’s facility in Moses Lake, Washington. The Moses Lake building is predominantly powered by hydroelectric power, a key factor in creating a sustainable product verified by third-party ecolabels including EPEAT.
Qcells began their US manufacturing efforts with their Dalton, Georgia, module manufacturing facility in 2019. The Dalton factory started with a capacity of 1.7GW annually, equivalent to the peak output of the Hoover Dam. Since then, Qcells has expanded its Dalton capacity, bringing its combined capacity to 5.1 GW. The company completed its latest expansion in 2023, adding 510 additional solar factory jobs, and will produce Qcells’ newest solar products: the Q.TRON G2 residential module and a bifacial module for the C&I segment.
The Impact of Bringing Solar Manufacturing Back Home
The term “solar coaster,” has been a long-time way of describing our expanding, yet truly dynamic industry. Met with episodes of supply constraints, evolving policy, and international trade issues, a strong case can be made for adding more dependability and stability amidst market uncertainties. Localized manufacturing can help rescind some of that unpredictability as manufacturers exercise tighter control over supply chains in the U.S.
Not to mention the profound economic ramifications. In its American Solar and Storage Manufacturing Renaissance report, SEIA predicts that 115,000 new jobs in solar and storage manufacturing will be created by 2030 due to the IRA and more than 507,000 new jobs across the broader industry, contributing over $100 billion to the economy. Qcells’ investments in building a vertically integrated solar supply chain are expected to benefit the local communities in Georgia, employing nearly 4,000 people between its Cartersville and Dalton factories.
The escalation of domestic manufacturing through the establishment of new and expanded U.S. facilities, coupled with the announcements from solar and storage companies regarding their plans for onshore manufacturing, indicates a concerted effort to fortify the market with reliable local supply chains. For questions or more information on solar supply chain localization and domestic manufacturing, contact your local Greentech Renewables today.