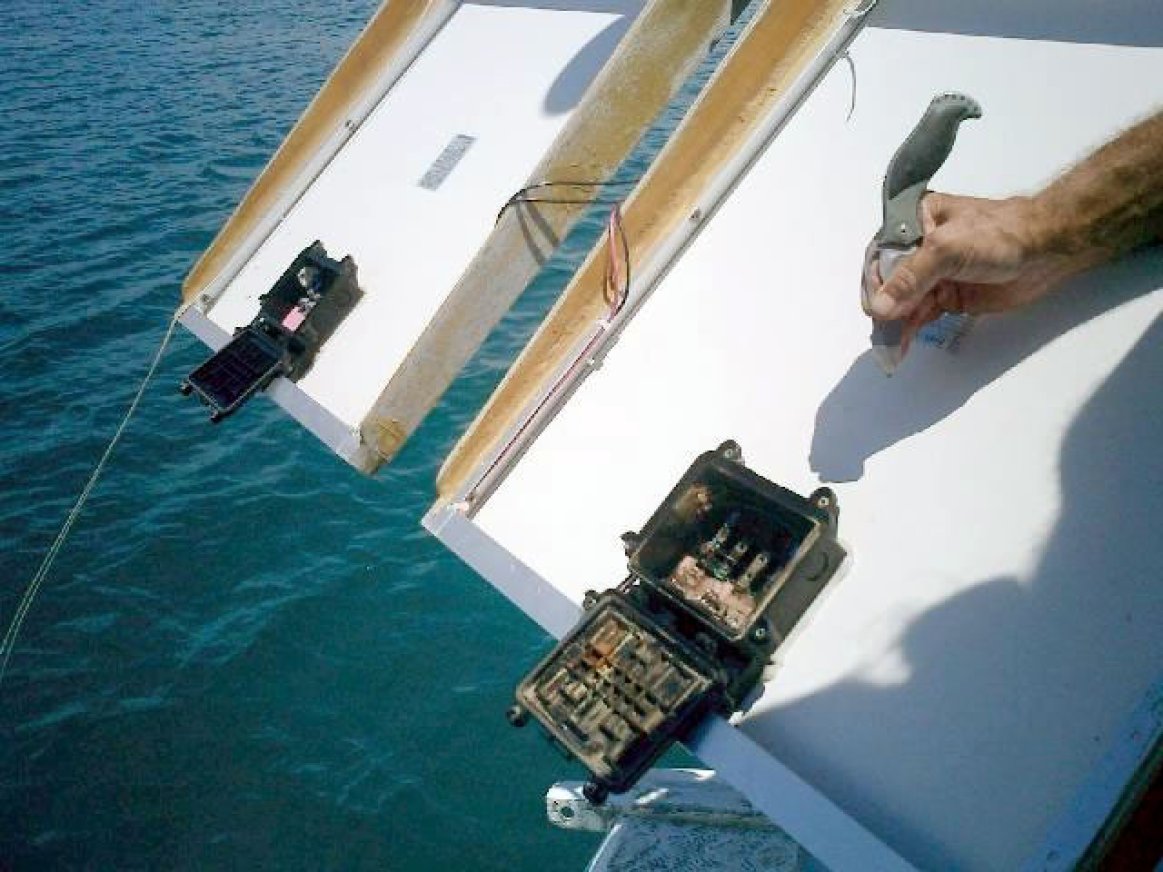
What is galvanic corrosion?
Galvanic corrosion is an electro-chemical process in which one metal type corrodes to another, occasionally causing structural failures in racking components. The metals in solar PV racking and mounting systems can be faced with corrosion if wrong metals are used together. The life of a solar PV system is 25 years, therefore system installers must target a similar life span for the racking materials.
How does galvanic corrosion occur?
In the event of galvanic corrosion, a galvanic circuit is created in which the anode (active metal) loses electrons to the cathode (noble metal) when both metals are exposed to an electrolyte (water). The nobility of the metal is the determining factor of corrosion. The more dissimilar metals are, the greater the corrosion potential is. As a rule of thumb, the solar installer has to avoid joining metals that are dissimilar in the Galvanic Series Table. (see below)
For example, steel alloy is more anodic (more active) next to stainless steel or aluminum alloy is anodic next to brass. It means that steel and aluminum corrode next to stainless steel or brass when an electrolyte and conductive way is present.
The risk of corrosion is also a factor of the environment. For example, moisture provides electrolyte that enables galvanic corrosion to occur. As humidity increases, the rate of corrosion increases. Also, the atmospheric contaminant catalyzes the chemical reaction. For example, chlorides (in marine environments) and sulfur dioxide and nitrous oxides (in industrial locations) provide a higher risk of corrosion.
How to avoid galvanic corrosion
In the solar industry, most of the racking system components (including the solar module frames) are either mill finish aluminum (aluminum alloy) or anodized aluminum (increased corrosion resistance). There are some bolts and nuts that are stainless steel, bronze or brass. The installer has to be careful in choosing the right material. We usually suggest using anodized components to prevent corrosion for the PV systems that are near ocean (salt conditions).
Below is a list of best practices for corrosion prevention:
- Use one material to fabricate electrically isolated systems or components where practical.
- If mixed metal systems are used, select combinations of metals as close together as possible in the galvanic series, or select metals that are galvanically compatible.
- Avoid the unfavorable area effect of a small anode and large cathode. Small parts or critical components such as fasteners should be the more noble metal.
- Insulate dissimilar metals wherever practical [for example, by using a gasket]. It is important to insulate completely if possible.
- Apply coatings with caution. Keep the coatings in good repair, particularly the one on the anodic member.
- Add inhibitors, if possible, to decrease the aggressiveness of the environment.
- Avoid threaded joints for materials far apart in the series.
- Design for the use of readily replaceable anodic parts or make them thicker for longer life.
- Install a third metal that is anodic to both metals in the galvanic contact
Galvanic Series (Corrosion Index)
Joining more dissimilar metals provide a higher potential for corrosion. The combination of an anodic and cathodic metal may eventually result in disintegration of the anodic metal due to constant loss of electrons.
Least Noble (Anodic) - Most Active |
Magnesium |
Zinc |
Aluminium alloys |
Low alloy steel |
Cast iron |
Lead |
Alumninum bronze, brass |
Copper |
Bronze (manganese, silicon) |
Nickel, Silver |
Stainless steel 302, 304, 316, Alloy 20 |
Titanium |
Gold, Platinum |
Graphite |
Most noble (cathodic) |
Sources: